10 Most-Common Mistakes to Avoid When Building a Log-Home
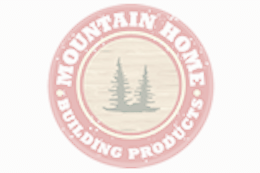
As with building any home, whether log style or traditional, it’s very easy to get caught up in the whirl- wind of the excitement and overlook some very important building considerations. Mistakes or oversights can be very costly to re-do or replace while other blunders are permanent—and living with a new log-home with features that can’t be fixed can be very regrettable.
Let’s take a peek at ten factors that are not always taken into consideration when building a log-home.
1: Log Placement Too Close To the Ground
If logs are at ground level or are too close to the ground, the longevity of those logs will be compromised. Continual water saturation from the ground due to hard rains or splattering due to rain or even sprinklers will bombard low-placed logs with too much moisture. Keep the first row of logs off the ground by at least 18 to 30 inches! Also, using an ice and water-shield product on the bottom-level logs will add extra protection from moisture.
2: Eliminating Larger Overhangs and Gutters
Perhaps you’ve seen log-homes with roof overhangs that seem oversized. There’s a reason for exaggerated overhangs and it boils down to protection from wetness. Design at least 24 to 30-inch overhangs on the sides and at least 4-6 feet overhangs on the ends. Your mission must be to keep the logs as dry as possible! People mistakenly feel it’s OK to use shorter roof overhangs in order to save money. What will end up happening is you will pay many times over in the long run due to log deterioration. Gutters and downspouts are not an option-- they must be in place as an added feature to keep logs drier.
3: Utilizing Too Much Wood
Yes, wood offers a natural-kind of richness that cannot be duplicated, but don’t make the mistake of over-doing the wood look. Wood floors, walls, ceilings, beams, cabinets and wood-accented furniture will end up becoming monotone overload. Be sure to break up any wood floors with tile and/or good-quality carpeting. Countertops with wood-grain appearance should be avoided at all costs. Instead choose colors or textures that are dissimilar to wood such as granite, colored concrete or stainless steel. What many people don’t realize is that sheetrock can be used in the dividing interior walls. Plastered walls can serve as a great contrast to the natural logs throughout the home. Don’t be sorry your whole home is wood, wood, wood---break it up with contrasting, yet complimentary, building materials that will provide deeper distinctions and eye-catching contrasts.
4: Logs Not Properly Prepped
Some people will make the mistake of not properly preparing the logs before they are stained. An element known as “mill glaze” can form on the surface of logs. Mill glaze is a glossy finish that is created due to water-soluble resins that rise to the surface. If this surface is not removed, it will cause major problems with finishing products adhering to the surface of the logs. Many Do-It-Yourselfers have found this to be true the hard way!
Additionally, logs should be water-proofed and insecticide-treated; and these applications should take place every few years, continually. If not, then you guessed it—moisture and pesky insects and spiders will find a breeding ground in which to multiply.
5: Using Logs Not Adequately Dried
Knowing the moisture-level of logs is crucial since moisture level is a major contributor to settlement in a log home. Logs that have a greater moisture-content will undergo a longer period of moving, twisting and shrinkage as the logs continue to dry. This, in turn, will leave gaps between the logs, creating air-leaks. Air-dried logs can still be about 15% to 20% water when the home is constructed; and ideally, logs should be allowed to dry in a protected area for a minimum of 6 months prior to construction! In fact, when it’s time to apply any oil-based stains, the log’s moisture level must be below 15%. It’s important to check the moisture levels of logs and this can be easily accomplished with a moisture reader.
6: Not Researching Log Home Kits
There’s nothing wrong with buying a log-home kit but there is one consideration that has come back to bite people in the end with kit purchases—sales tax! Yep, most states charge a sales tax on log-home kits. This can easily add up to 10% of the cost of the kit and an unexpected bill of $6,000.00 to $10,000.00 can become a monetary nightmare. This can be avoided if one chooses to build a log-home from scratch, instead.
7: Not Utilizing Concise Construction Plans
If one is utilizing a professional builder for their log home, the only way to get an accurate bid is to have accurate construction plans which, by the way, are different than floor plans. If one has not done one’s homework, one can offer a vague construction plan that is very imprecise in specifications of building materials and methods. This, unfortunately, can leave a homeowner unprotected in that the builder may have his own interpretation of the choice of materials or methods to be used. That can cost the homeowner much more than expected.
8: Inadequate Pre-Construction Planning
Everything that has been mentioned, so far, would fall under the category of inadequate pre-construction planning. If one is building one’s own log-home, then research and more research is a pre-requisite to avoid any pitfalls that are just waiting to happen. Comments such as, “Are you kidding me?!” or “So, how do we fix this fiasco?!” or “Maybe we should’ve hired a professional, after-all!” shouldn’t be a part of one’s home-building experience. There will be challenges no matter what, but if lack of knowledge and insight take the place of copious study, careful examination and detailed evaluation, then problems can become insurmountable. All too often, a project can end in disaster as one learns, too late, that log-home construction can be much more complicated than it may have appeared. Sometimes, it’s simply best to leave the construction of a log-home up to a professional unless one truly has the time and the knowledge required to get the job done right. Unfortunately, too many people overlook the importance of finding a qualified builder for their log home and settle for the lowest price instead.
9: Not Hiring an Inspector
A log-home is just like any other investment, such as a car—it requires regular maintenance to ensure longevity. Hiring a professional inspector to assess interior or exterior features of a log-home will ensure the home’s beauty and structural integrity are never compromised.
- An inspector will assess things such as:
- the presence of mold or fungus
- separation of joints
- the condition of chinking
- grading and water-flow away from the home
- separation between log walls and interior ceilings
And this is just a partial list! A home is a big investment, and not hiring a professional inspector can allow unseen problems to linger and compound.
10: Choosing Not To Use Energy-Efficient Materials/Appliances
It’s certainly true that we would all want to save as much up-front money as possible if we were in a positon to build a new home, but saving money up front should never trump saving money in the long-run. Too often, energy-efficient appliances, windows and HVAC systems are down-graded to keep more money in one’s pocket; but if truth be known, EnergyStar appliances and building materials, for example, provide unsurpassed air-sealing and insulation levels and superior energy-efficiency that make a noticeable dent in monthly utility bills. When inferior materials are part of the plan, energy costs go up.
There’s so much to think about when it comes to building a log-home; but buyers’ remorse and personal regrets don’t have to enter the equation. Do your homework, hire a reputable builder if necessary, invest a bit more in quality building materials and keep up on maintenance schedules—in the end, you’ll find that the word ‘mistake’ is one word you won’t have to deal with!